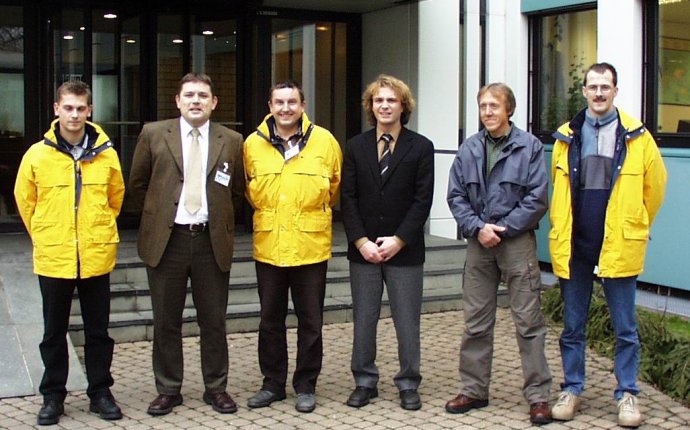
Bosch Rexroth Belgium
Perovskite PV technology demonstrated on industrially-applicable roll-to-roll processes
Eindhoven (the Netherlands), Leuven (Belgium), March 9, 2017 – Solliance announces the demonstration of an industrially-applicable roll-to-roll process for the production of solar cells, achieving a record 12, 6% conversion efficiency on cell level. This breakthrough result paves the way towards an accelerated market introduction of this attractive new source of renewable energy.
Perovskite microcrystals are a promising material to make high-yielding, thin-film solar cells. They can be processed into thin, light-weight and potentially semitransparent modules that could eventually be integrated in building materials such as windows or curved construction elements. Solliance and its research partners focus on using scalable, industrial processes towards the fabrication of large-area modules, eventually suitable for seamless integration in a broad variety of PV systems.
The roll-to-roll (R2R) process was developed for both the electron transport and the perovskite layers on the new Solliance dual R2R coating line, as developed by Solliance with its partners VDL Enabling Technologies Group (VDL ETG), Smit Thermal Solutions and Bosch-Rexroth. The in-line roll-to-roll coating, drying and annealing processes were executed at a linear speed of 5 m/min on a 30-cm wide commercial PET/ITO foil and under ambient conditions. After applying a newly developed off-line single device finishing step, individual solar cells of 0.1cm2 achieved efficiencies of up to 12, 6%, measured under maximum power point tracking conditions during 5 minutes. All process steps on this roll-to-roll line were performed using low cost materials whilst keeping the process temperatures below 120 ⁰C. This shows the high volume production potential of this new emerging thin film PV technology.
“The demonstration of R2R processing at 5 m/min of perovskite layers for solar cells indicates that high-volume production, and hence with an expected very low cost, will be possible in the future”, explains Pim Groen, Professor of SMART materials at the Technical University of Delft and Program Manager at Holst Centre/Solliance. ”These results show that the Solliance research partners, with their in depth know-how on processing of thin film PV devices and their extensive sheet-to-sheet and roll-to-roll pilot production infrastructure, are excellently placed to realize this upscaling.”
VDL ETG has been leading the consortium of equipment manufacturing companies that designed and built the innovative R2R coating line. VDL’s CEO Willem van der Leegte comments: “I am very pleased with this result. It shows that combining process know-how at Solliance with capabilities of high-tech equipment companies in this region can deliver very powerful results that potentially open up completely new business opportunities.”
Richard Caldwell, Managing Director remarked: “Dyesol is very pleased with this breakthrough; we are committed to developing the industry standard for R2R Perovskite Solar Cell (PSC) PV manufacturing in conjunction with Solliance and this result is an important step along this route. This pioneering work confirms that Dyesol and its partners retain a global leadership position in the industrialisation of PSC Technology, and in particular, its continuous R2R processing for flexible BIPV applications – a core element of its commercialization strategy.”
The current world record efficiency of a small lab scale perovskite-based PV cell is 22, 1%.
“The challenge is to upscale perovskite cells to larger size, industrially-manufacturable modules with high efficiency and long lifetime at low cost. These 12, 6% R2R up-scaled perovskite-based solar cells are a first and important step in this development. With this result, we are confident to quickly boost the up-scaled perovskite based PV module efficiency above 15% by using low cost materials and processes. Furthermore, we are working hard to improve the stability of these devices under real life operational conditions”, explains Ronn Andriessen, Program Director at Solliance.